Design
Neal Aronowitz
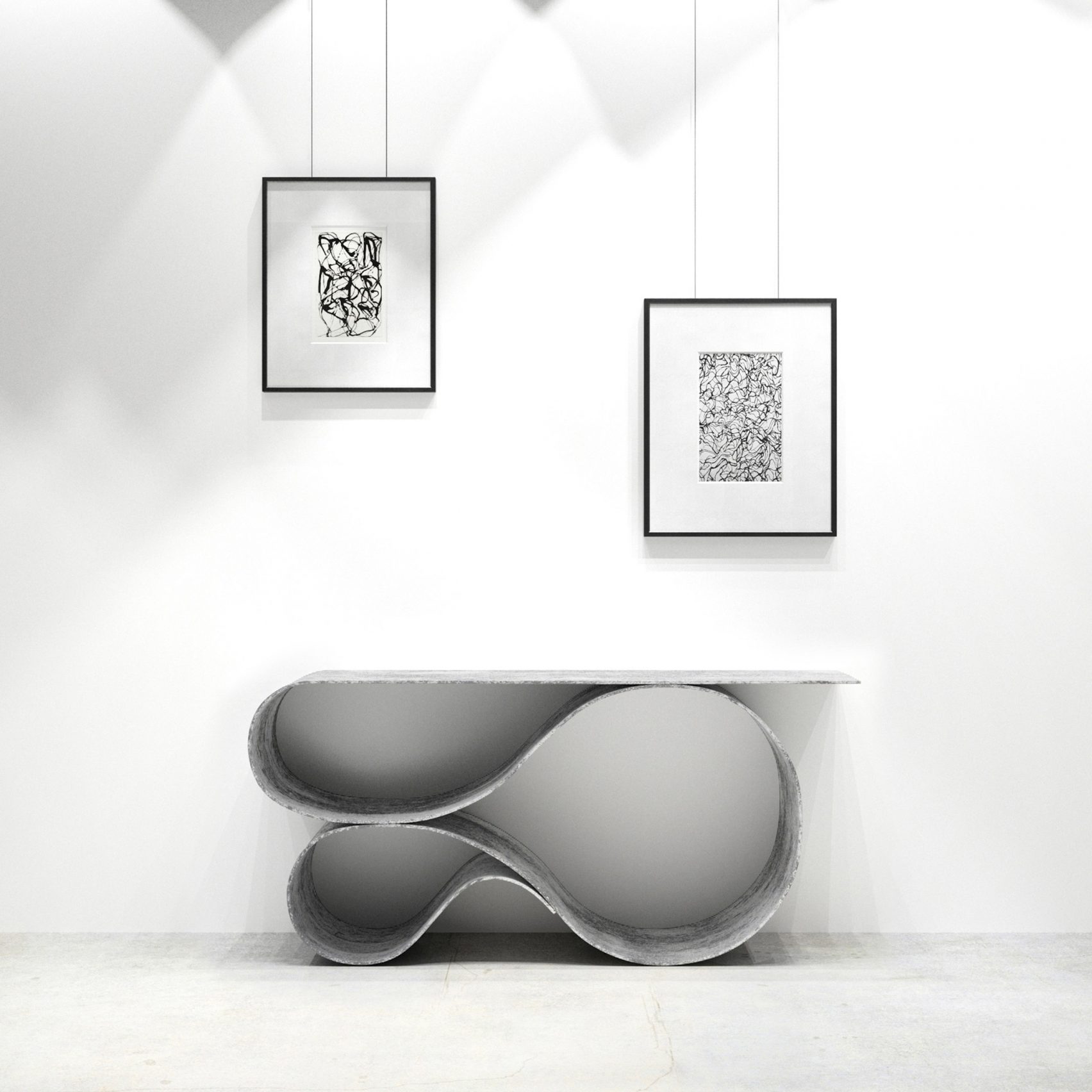
Whorl Console, created from a patented material by the UK company, Concrete Canvas.
Image courtesy of: Dezeen
For the Portland-based Neal Aronowitz, creating highly-sculptural, hand-crafted furniture is a dream. He looks forward to waking up each morning and designing with a special, patented material called Concrete Cloth. Once familiar to the public, it did not take long for the international design world to fall in love with Aronowitz’s work; in 2009, Concrete Cloth won the award for Material of the Year.
Up until that time, the material was used for rapidly deployable shelters; that was because the substance could be easily manipulated from roll-out strips. However once Aronowitz began to experiment with the Concrete Cloth, he opened up a whole design method.
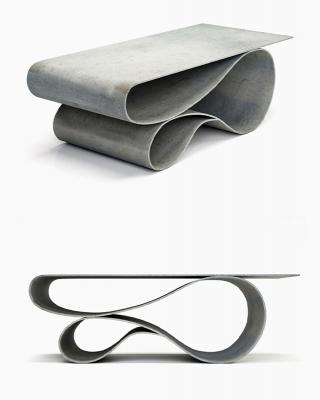
Whorl Table, 2014.
Image courtesy of: Neal Aronowitz (as featured in Pamono for Charish)
It was a decade after graduating from New York City’s City University that Aronowitz began designing and building furniture as a side gig. He mainly worked on pieces for private clients. In 1996, the designer relocated to Portland and began to make furniture on commission until he formally debuted his studio in 2014.
The first pieces, the Whorl Coffee Table and the Whorl Console, to come out of the studio were from the Concrete Canvas Collection. Aronowitz became known as the only designer to work with this innovative and pliable material. Seeming to defy gravity, the sculptural piece is composed of a single sheet of canvas made from concrete… folding and molding as though a fabric. Quickly, the collection became a hit; it has won numerous design awards including Interior Design Magazine Best of Year for residential furniture.
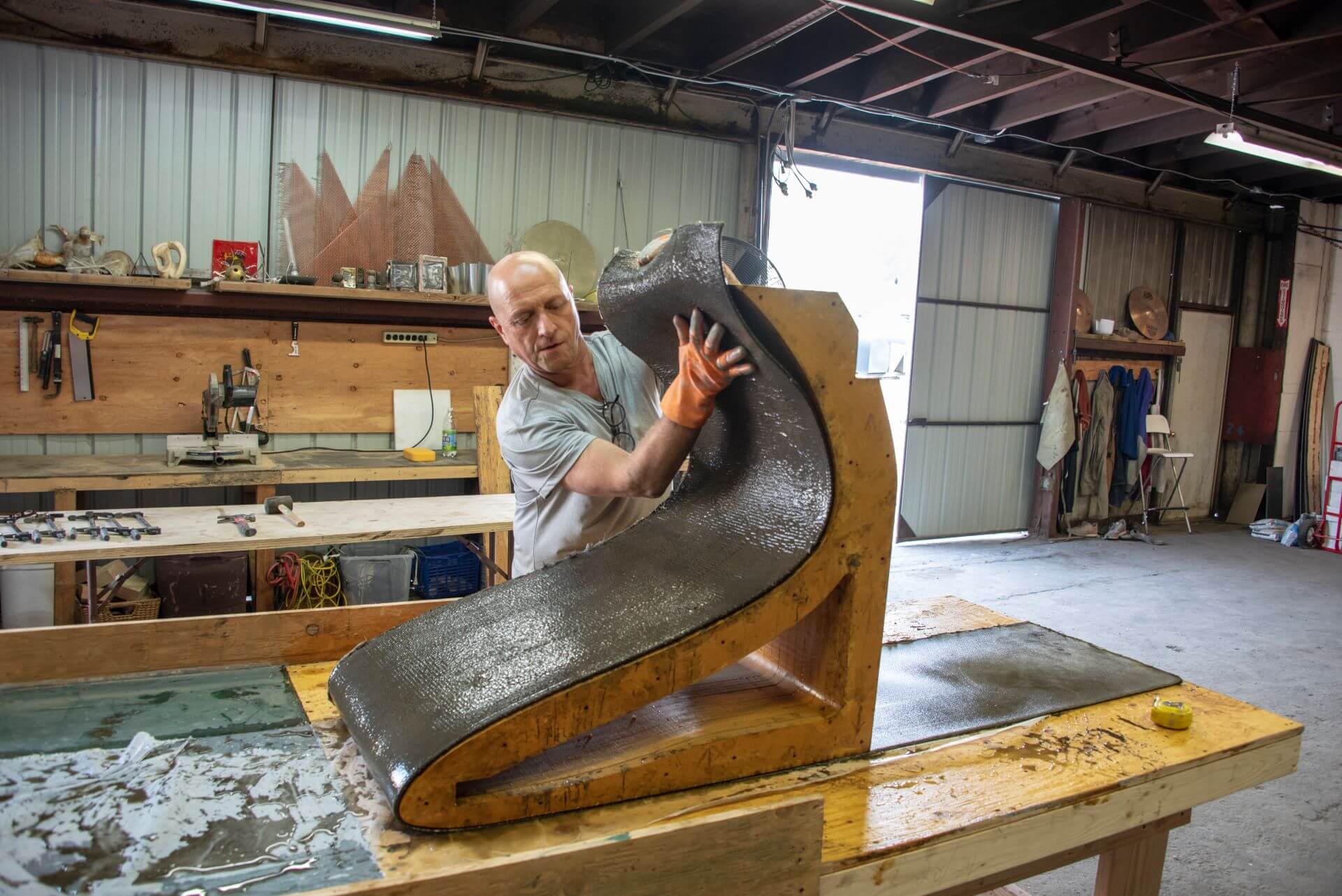
As Aronowitz explains (courtesy of Design Wanted), “Essentially it is concrete cloth on a roll.”
Image courtesy of: Neal Aronowitz (as featured in Design Wanted)
Part of the beauty behind the material is that it is both eco-friendly and high-tech. Courtesy of Dezeen, Aronowitz said, “It reduces the environmental impact of concrete applications by up to 95 per cent.” With the collection, the designer hoped to “explore the material’s unique structural properties to express a fluid form, in contrast to the dense and heavy associations that we have with concrete.”
The cloth-like material is formed when fabric is “impregnated” with cement. The effect hardens upon hydration to form a thin, pliable, fire-resistant, and waterproof layer. Aronowitz has been able to push the boundaries of the material’s tensile strength; however he has always remained cognizant of retaining his specific vision for the aesthetic.
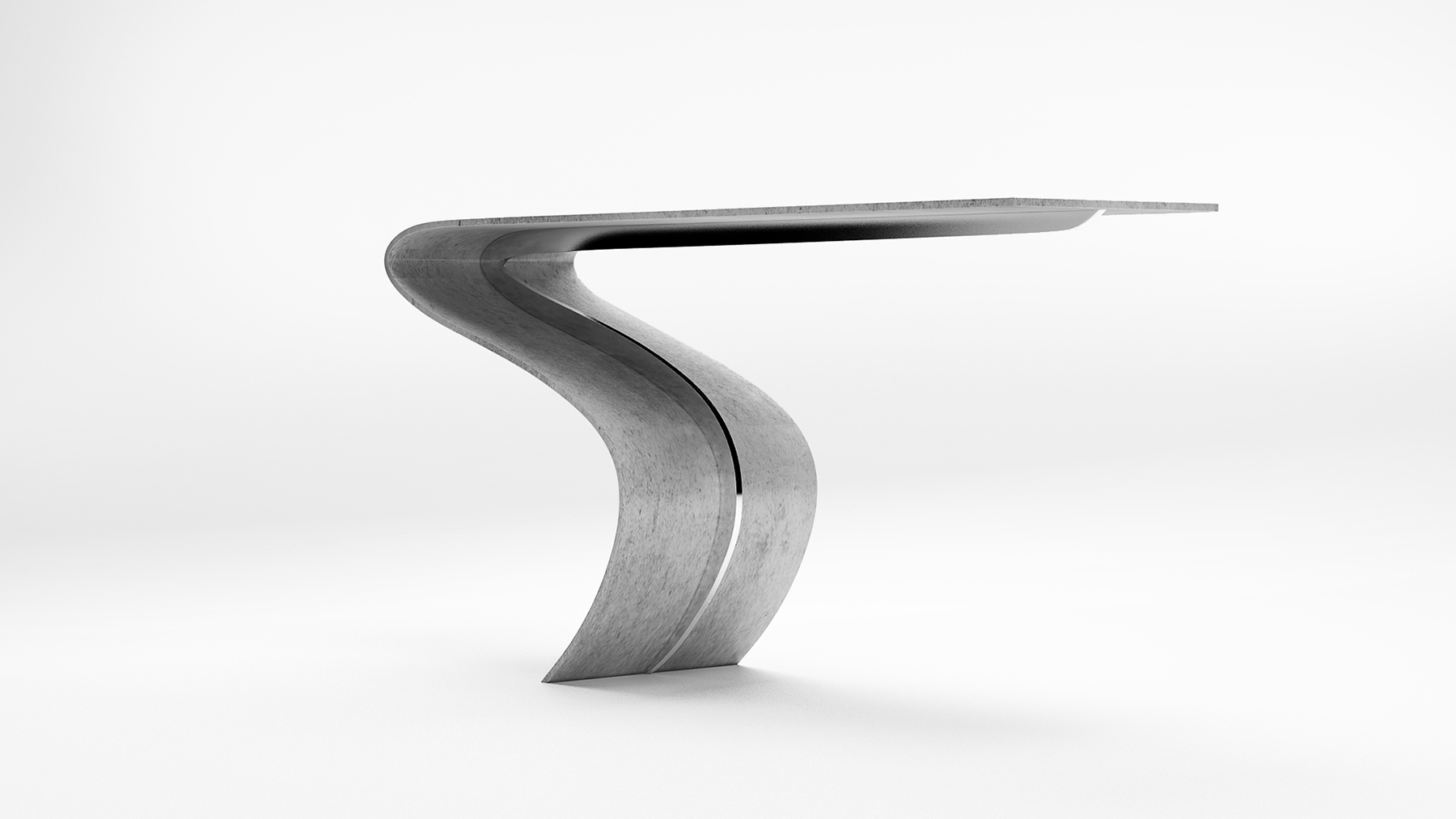
Enso Console, a wall-secured piece made from Concrete Canvas, polished aluminum, cement mortar, and cement pigments.
Image courtesy of: Neal Aronowitz (as featured in Ignant)
Aronowitz followed up the Concrete Canvas Collection with the Enso Table. With this furniture piece, the designer drew inspiration from the practice of ancient Japanese ink painting. A function of creativity and a display of free expression, the table looks as though it was made in one swift, fluid stroke.
It was new casting and forming techniques using custom-made wooden molds that allowed Aronowitz to successfully debut this piece. The ribbon-like structure was the result of many experimental attempts.
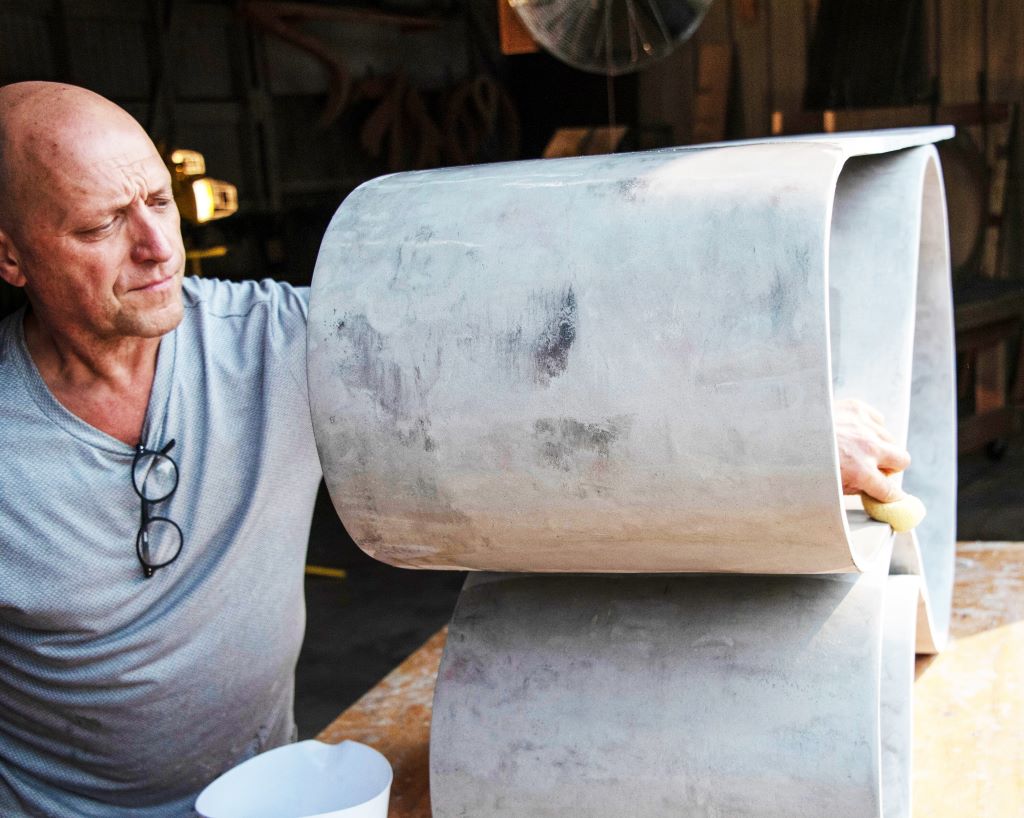
The final steps, including sanding and sealing.
Image courtesy of: Neal Aronowitz (as featured in Design Wanted)
Through his experimentation, Aronowitz developed a very specific, five-part wooden mold to accommodate the Concrete Canvas. However first, the material is cut from the roll and the cut ends are sealed to ensure that the concrete does not “escape” from the canvas during the fabrication process. When this is finished, the concrete is immersed in water to give it the pliability to take on unique, ribbon-like shapes. For this process, Aronowitz built a 22-foot-long trough.
As the material is wrapped around wooden molds, it is clamped into position. With time of the essence (there is only half an hour before the material becomes too hard to manipulate), the design is created and the piece is covered in plastic and left to dry overnight. In the morning, the molds are removed; thereafter, the piece is reinforced with a wire mesh and covered with cement mortar… this gives the structure additional strength.
Finally, the piece is custom colored with cement pigments to create a finish that mimics concrete. The final step is to seal the surface in order to prevent staining. It can take up to 125 hours of work to complete a single piece of furniture… again highlighting why art and design are really one of the same.